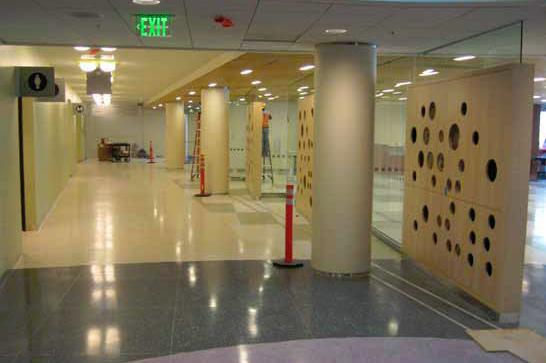
With today’s economy affecting corporations all over the world, most firms are trying to use their resources wisely. Rob Harris investigates one company that has incorporated a strategy that has taken it to the next level.
On January 17, 1994, at 4:31 am Pacific Standard Time, the city of Los Angeles was hit by a major earthquake that lasted about 45 seconds. It was recorded as magnitude 6.7, wreaked over $20 billion in damage, caused 72 deaths, and significantly changed the way building construction was approached in the state of California.
On February 25, 1994, California Senate Bill 1953 was introduced, and it was signed into law on September 21, 1994. This bill was an amendment to the Alquist Act of 1973 and specified that if a hospital were to remain an acute care facility, the owner must conduct seismic evaluations and prepare both a comprehensive evaluation and a compliance plan to the specifications mandated by the California Office of Statewide Health Planning and Development (OSHPD).
Childrens Hospital Los Angeles was one of approximately 470 general acute care facilities affected by this legislation. Childrens Hospital Los Angeles knew that this project was going to be difficult, long and complicated. In 2003 the hospital hired Rudolph and Sletten.
Onslow H. Rudolph started as a general contractor in 1959 based out of his family garage in Los Altos, California. He began with a small amount of savings, a pickup truck and two employees. The business grew quickly and became well known for its ability to delivery high-quality work on time and within budget. In 1962 Kenneth G. Sletten joined as a business partner and the company was renamed Rudolph and Sletten. In 2005, Rudolph and Sletten was acquired by Tutor Perini Corporation, one of the largest construction services companies in the US.
Today, Rudolph and Sletten is one of the largest contractors on the West Coast. With 38 percent of its staff already LEED accredited, the company has the highest percentage of LEED Accredited Professionals in the US and has set a goal to have 100 percent of its managers accredited. Incorporating Building Information Modeling (BIM), Integrated Product Delivery (IPD) and lean construction methods, Rudolph and Sletten continues the company’s legacy of fine craftsmanship and superior customer service in every job it does.
In 2006 construction began on the new 317-room, 480,000-square-foot hospital building of Childrens Hospital Los Angeles. This facility, when completed, will not only feature mostly private rooms but also incorporate new inpatient and surgical suites, new neonatal and pediatric intensive care units, a new cancer center, a new family education center and a new conference center. The original project design started in 2003.
Full-scale mock-ups of the PICU, NICU and acute patient rooms were built using a variety of proposed finishes, such as floors, paneling, counters and bathrooms. A group consisting of patients, parents and caregivers provided valuable feedback, improving functionality and increasing comfort. Matt Bennett, senior project manager, states, “We spent three years in pre-construction. We constructed a building to house the patient room mock-ups near the hospital so the different user groups could walk through and see what the rooms were going to look like and how they would operate. The client allowed us the opportunity to incorporate early involvement from the key subcontractors throughout the planning and design phase, which assisted in meeting the schedule dates and the budget.”
As with any project of this size, there were many challenges that had to be overcome. The State of California regulations related to the planning, design and construction of hospitals, as administered by the OSHPD, require rigorous attention to detail and construction execution. As Bennett explains, “OSHPD has very specific requirements for building a hospital. Continuous inspections including seismic and fire life safety requirements, adherence to applicable codes and standards while maintaining an efficient and productive jobsite were the most challenging aspect of constructing a hospital of this magnitude.” To meet these requirements, Childrens Hospital Los Angeles’ management, Rudolph and Sletten, and the owner’s representative, CLEO Construction Management, partnered with OSHPD early and throughout in the project by communicating the project’s plan for obtaining the necessary design approvals, agency reviews, construction inspection and acceptance and ultimately occupancy.
Not only did the project face regulatory challenges; it also faced economic ones. “The project team through a collaborative effort overcame market conditions with double-digit escalation, delayed state funding, shortage of skilled tradesmen as well as furloughs from OSHPD. Bennett says, “This project was a total team effort. We all supported each other to ensure a win-win for everyone.”
Proper planning can make the difference in the success or failure of any project. Rudolph and Sletten has incorporated into its business management style the philosophy of lean construction, a production management-based approach to project delivery, and it changes the way work is traditionally done through the delivery process. Lean construction takes the objectives of a lean production system—the application of processes to maximize value while minimizing waste—and applies them in the project delivery process. Lean construction began with the insight that regular project-type planning systems did not have the ability to produce a predictable work flow and that the project needed to be designed and managed by those responsible for getting the job done.
Bennett explains how lean construction was incorporated in this project. “We did a lot of prefabrication of systems. All the overhead plumbing was detailed and cut to fit in the shop and then brought out in a kit. All the seismic braces, pipe runs, custom headwalls and a lot of the electrical were prefabricated off-site. We worked very closely with the major contractors when we built the schedule.” The value of lean construction shows in the fact that the project is set to be finished this September, on time and on budget.
Thomas A. Edison said, “Waste is worse than loss. The time is coming when every person who lays claim to ability will keep the question of waste before him constantly. The scope of thrift is limitless.” Good companies know that waste is worse than loss, and those companies try to incorporate plans and philosophies into their missions that facilitate responsible management and planning. Rudolph and Sletten is one of those companies that, by using innovation and trying new techniques, is keeping its business model the same: delivering the highest-quality work, on schedule and within budget.